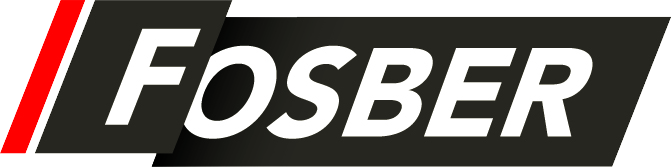

COMPLETE CORRUGATOR

ROLL STAND & SPLICER - STAND M2 & LINK
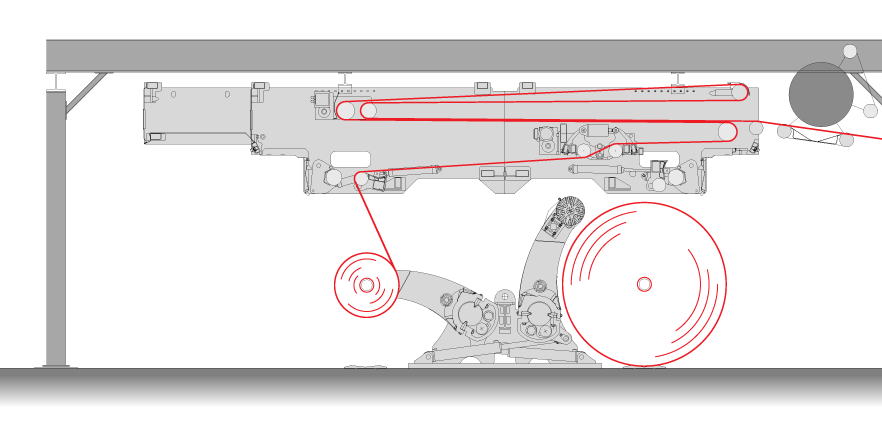
- Intro
- Gallery
I porta bobine e le giuntatrici Fosber sono pensati per garantire flessibilità, velocità, affidabilità ed elevata produttività.
La Link giuntatrice offre una tecnologia innovativa disegnata per effettuare una giunta con precisione ed affidabilità. Può essere integrata con il porta bobine STAND M2, disponibile nella versione automatica e semi-automatica di caricamento, per una gestione completa del ciclo bobina.
La giuntatrice Link offre un sistema doppio di preparazione della giunta che consente di lavorare in velocità e sicurezza nella fase di applicazione dell’adesivo. La giunta preparata è automaticamente spostata nella posizione corretta eliminando eventuali errori umani e riducendo la presenza dell’operatore sulla linea. La posizione di giunta fissa assicura, inoltre, un efficace controllo del sistema di giunta automatico in caso di rottura carta (Tail link).
La giuntatrice automatica LINK offre, oltre ad una tecnologia di giunta innovativa, precisione ed affidabilità attraverso un disegno superiore. Per una completa gestione del ciclo bobina, è disponibile anche il porta bobine STAND M2, in versione a caricamento manuale o semiautomatico.
La doppia preparazione della giunta, la testa di giunta doppia mobile, il rullo acceleratore ed un doppio festone di scorta sono le sue caratteristiche principali.
Le due zone di preparazione giunta sono fisse e si trovano alle due estremità della macchina garantendo così una semplice, veloce e sicura preparazione della giunta per l'operatore.
Ciascuna delle due zone di preparazione è composta da un rullo di contrasto, una barra di supporto per la preparazione della giunta e da una barra di bloccaggio carta che serve appunto a mantenere la carta in posizione mentre l'operatore applica l'adesivo senza l'ausilio di alcun sistema di aspirazione.
L'operatore, una volta posto l'adesivo, deve soltanto confermare l'avvenuta preparazione premendo un pulsante. Il sistema sposta automaticamente la giunta preparata nella corretta posizione eliminando così qualsiasi eventuale "errore umano". La posizione di giunta fissa assicura un accurato ed efficace controllo del sistema TAIL LINK (giunta automatica in caso di rottura carta). Le due teste di giunta mobili sono a bordo di un carrello motorizzato dove sono presenti le due lame di taglio, i rulli incollatori, i rulli di contrasto mobili ed i freni tampone.
Il carrello allinea automaticamente la relativa testa di giunta in corrispondenza di una delle due zone di preparazione per procedere poi alla giunta. Una volta attivato il ciclo, il freno scende automaticamente a fermare la carta in lavoro. A questo punto, con un unico movimento di un cilindro pneumatico, la lama penetra nell'apposita feritoia tagliando la carta della vecchia bobina, mentre il rullo di contrasto mobile ed il rullo "incollatore" entrano in contatto per creare un incollaggio perfetto tra le due carte e l'immediato sblocco delle stesse. L'azione simultanea produce un accurato incollaggio tra le carte in un tempo di soli 0.25 secondi. Il risultato finale è una reale sovrapposizione tra le carte ben incollate il tutto alle massime prestazioni.
Un motore vettoriale controlla il rullo acceleratore posto all'uscita delle carte per migliorarne la ripartenza e la tensione costante. Questo rullo ha sia la funzione di frenatura della carta della vecchia bobina, che quella di riportare rapidamente la carta della nuova bobina alla velocità di linea. Il rullo acceleratore lavora in perfetta sintonia con il "ballerino" con l'obiettivo di monitorare e mantenere sempre costante la tensione della carta. Il preciso ed accurato controllo del "ballerino" permette, anche durante il ciclo di giunta, una perfetta tensione della carta in relazione alla velocità della linea.
Il quadro elettrico integrato è munito di uno schermo grafico d'interfaccia con il quale l'operatore può visualizzare tutti i principali parametri della macchina e gli eventuali guasti/malfunzionamenti. La macchina è completamente protetta e certificata CE.
STAND & SPLICER INTEGRATI - LINK M3
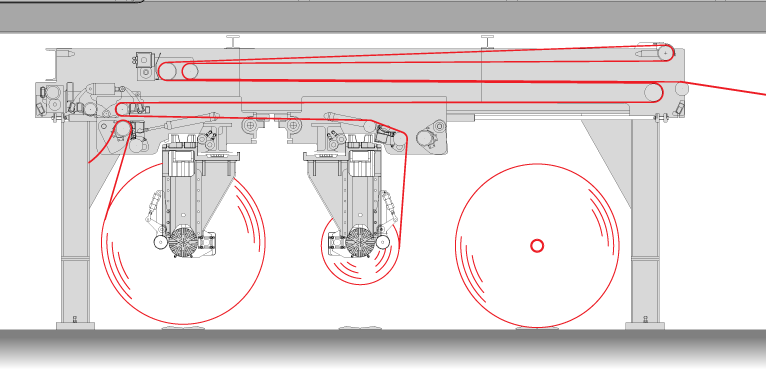
- Intro
- Gallery
Il porta bobine e giuntatrice Link M3 rappresenta una soluzione integrata unica nel suo genere per una gestione ottimale delle bobine di carta sull’ondulatore, garantendo il più breve ciclo completamente automatico di cambio bobina disponibile nel settore. Con la nuova tecnologia Link M3, il posizionamento dell’ondulatore diviene irrilevante, infatti, anche quando situato vicino ad una parete non si ha nessun impatto sulla velocità del ciclo bobina (70% meno dei sistemi convenzionali) dato che la gestione delle bobine è totalmente contenuta su un lato della linea.
La Link M3 è una macchina indipendente, costituita da una solida struttura modulare che funziona anche da supporto per il ponte. Il porta bobine dispone di tutte le più recenti caratteristiche tecniche che consentono il centraggio e l’allineamento automatico delle bobine prima di essere caricate dai bracci meccanici. Tali bracci, sono indipendenti l’uno dall’altro ed eseguono automaticamente il sollevamento delle bobine consentendo l’allineamento meccanico della carta. I bracci sono dotati di un espulsore automatico di anime e di freni multi - disco di ultima generazione che garantiscono un controllo omogeneo della tensione della carta. Inoltre, i bracci sono dotati di un avvolgitore automatico che consente, dopo la giunta, di riavvolgere meccanicamente le bobine in uscita dall’area della Link M3. L’operatore preparata la giunta può abbandonare l’area di lavoro e dedicarsi ad altre attività diminuendo il fabbisogno generale di manodopera sul wet-end.
La giuntatrice all’avanguardia della Link M3 comprende un rullo acceleratore per frenare in sicurezza e rapidità la carta in uscita e accelerare rapidamente la carta della nuova bobina alla velocità di linea. Il rullo acceleratore lavora in perfetta sintonia con “il ballerino” con l'obiettivo di monitorare e mantenere sempre costante la tensione della carta.
La Link M3 sfrutta una tecnologia innovativa, Fosber ha brevettato una testa di giunta che utilizza un unico semplice movimento meccanico per completare la giunta senza complicazioni di ciclo. Il risultato è un perfetto incollaggio delle due carte ad elevate velocità con massima affidabilità di giunta.
STAND & SPLICER COMPATTO - PAPERLINK
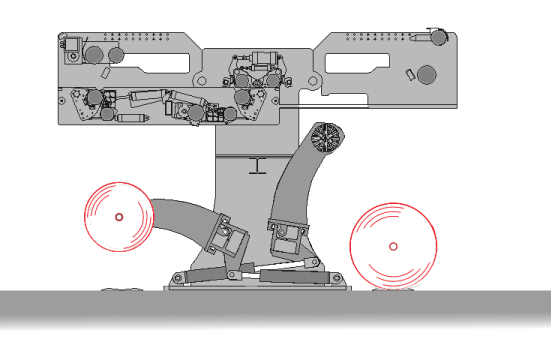
- Intro
- Gallery
La PaperLink è la nuova soluzione Fosber che integra porta bobine e giuntatrice in un’unica macchina.
È disponibile in due versioni: velocità di giunta 250 m/m (lunghezza 4m) o 300 m/m (lunghezza 5m).
L’innovativo design riduce l'ingombro della PaperLink e ne consente anche la compatibilità con ponti di altezze inferiori, abbattendo inoltre i tempi di installazione e i costi di trasporto.
La PaperLink ha una testa di giunta fissa, posizionata al centro della macchina e un carrello mobile inferiore che si sposta sui due lati esterni della macchina per una facile preparazione. La sequenza di giunta brevettata viene eseguita in un unico movimento continuo.
I due bracci integrati sono in grado di gestire bobine da 3,7 T e da 4,2 T con il doppio cilindro idraulico.
L’opzione Automation Pack permette il caricamento e lo scaricamento automatico delle bobine, completo di espulsori integrati.
L'opzione TAIL LINK prevede l'installazione di fotocellule su tutti e quattro i bracci per rilevare e avviare automaticamente la giunta di fine bobina o per eseguire automaticamente una giunta in caso di rottura della carta.
La PaperLink può essere dotata di un proprio quadro elettrico indipendente e di una console operatore.
GRUPPO ONDULATORE - SMART
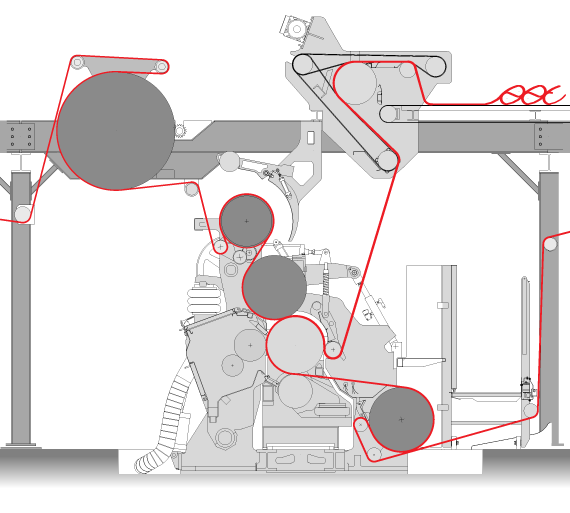
- Intro
- Gallery
Il single facer SMART dispone di un cambio rapido di cartuccia e di una struttura portante molto pesante in un'unica fusione di ghisa. La costruzione imponente con un basso centro di gravità, riduce enormemente le vibrazioni, assicurando un'ottima lavorazione con tutti i tipi d'onda a qualsiasi velocità.
Il cilindro pressa superiore è dotato di un sistema di regolazione della pressione graduale e preciso; per ridurre le vibrazioni è posto leggermente disassato rispetto alla verticale. Il cambio cilindri può essere eseguito da entrambi lati della macchina in soli 10 minuti tramite l'utilizzo di un carrello motorizzato.
Il single facer SMART non è equipaggiato con apparecchiature idrauliche che, invece, sono state poste sul carrello d'estrazione. Questa semplificazione ha reso la macchina più affidabile. Il differente diametro dei cilindri ondulatori riduce notevolmente le tensioni all'interno del labirinto di formazione dell'onda, migliorandone la qualità. Il riscaldamento periferico dei cilindri ondulatori, pressoché istantaneo, è ottenuto avvalendosi di canali periferici di volume ridotto, per questo non c'è bisogno dei classici sistemi a sifone per il recupero della condensa. Il vapore viene prima introdotto attraverso il cilindro ondulatore superiore, per passare successivamente all'inferiore e per ultimo nel cilindro pre-condizionatore, dove viene tolta la condensa. I cilindri ondulatori vengono forniti cromati o con rivestimento al tungsteno, secondo la preferenza del cliente ed il tipo di onda. Grazie al sistema "extended nip", la carta è mantenuta tesa e bene in contatto con il cilindro superiore per un tempo molto lungo senza l'utilizzo di tappeti. Il maggior tempo favorisce l'incollaggio permettendo così di poter lavorare con una leggera pressione del cilindro pressa. Il minor schiacciamento conserva le caratteristiche fisiche/meccaniche delle carte, quindi anche la robustezza del prodotto finale potrà essere notevolmente superiore. Grazie a questo dispositivo le linee di pressione sono in pratica eliminate.
La "camera di pressione positiva" mantiene bene aderente la carta al cilindro ondulatore garantendo un uniforme trasferimento di calore su tutta la larghezza della carta, conseguentemente un costante e ben distribuito film di colla. Nel progetto di SMART, il rullo applicatore della colla è posto perfettamente a 90 gradi rispetto al cilindro ondulatore e di conseguenza alle creste delle onde. Un dispositivo automatico verifica e mantiene costante lo spessore del film di colla impostato a qualsiasi velocità e con qualunque grammatura di carta. Le squadre laterali di contenimento della colla hanno un controllo automatico ed indipendente, oltre a questo un dispositivo automatico mantiene puliti i bordi dei cilindri ondulatori. Per semplificare la pulizia e la manutenzione, l'intero gruppo colla ruota allontanandosi dal corpo principale tramite la semplice pressione di un pulsante. Il dispositivo di controllo incorpora tutte le funzioni della macchina che possono essere visualizzate su un touch screen d'immediata comprensione. Pagine dedicate mostrano lo stato della macchina, gli eventuali allarmi ed i settaggi tecnici. Un sistema intelligente provvede automaticamente ed istantaneamente ai settagli di macchina ideali alla lavorazione di qualsiasi tipo di carta.
Il risultato è, una elevata flessibilità, una ottima qualità di prodotto a qualsiasi velocità e con qualsiasi tipo di carta.
INCOLLATORE - MPH & CREST
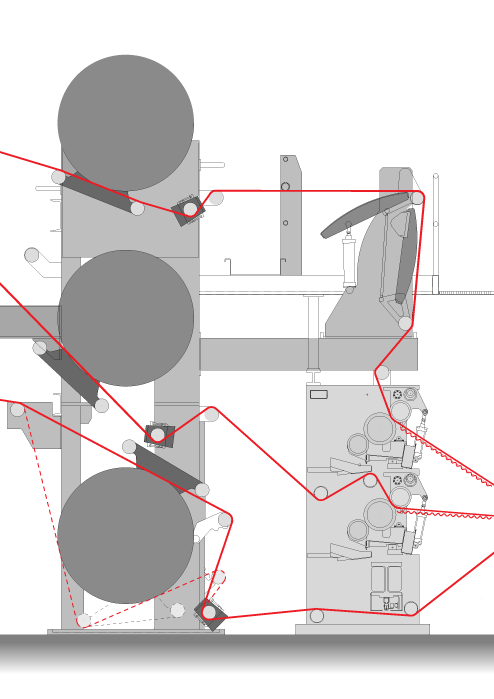
- Intro
- Gallery
L'incollatore CREST unisce produttività e velocità e qualità con ogni tipo di cartone. Flange eccentriche su entrambi i lati della macchina garantiscono il corretto parallelismo tra il rullo applicatore ed il rullo di controllo dello spessore di colla.
Il controllo micrometrico dello spessore di colla è ottenuto tra il rullo applicatore di colla (300 mm.) e il rullo dosatore (200 mm.) ed è garantito da un azionamento servoassistito la cui tolleranza è di 0,03 mm.
Il rullo applicatore retinato ed il rullo dosatore di controllo dello spessore di colla hanno una motorizzazione unica.
Il controllo dello spessore di colla è automatico e segue una curva variabile in funzione della velocità di lavoro, in maniera da mantenere costante la quantità di colla realmente applicata a tutte le velocità di lavoro.
Per mantenere aderente l'onda scoperta al rullo applicatore di colla si può scegliere di installare sia la "barra di contatto" che il rullo di aderenza (200 mm. cromato).
Particolare attenzione è stata dedicata alla realizzazione del "sistema colla". Le paratie di contenimento dell'amido all'interno della vasca, motorizzate indipendentemente, prevengono spruzzi ed un sistema automatico di lavaggio garantisce pulizia e precisione di incollaggio. L'ingresso dell'amido nella vasca di contenimento è centrale, mentre l'uscita e sull'intera luce della vasca per cui, il livello dell'amido mantenendosi costante contribuisce all'invariabilità della pressione idrostatica ed un costante consumo di amido.
I quadri elettrici a bordo semplificano l'installazione ed un pannello tattile fornisce informazioni precise sul settaggio della macchina; in caso di anomalia segnala allarmi ed una corretta diagnosi. Pulsanti di regolazione sono disponibili per le funzioni principali.
PIANI CALDI - EXPRESS

- Intro
- Gallery
La moderna tecnologia su cui si fonda il progetto permette di poter produrre cartone di diverse grammature fino ad una larghezza di 2800 mm.
La tecnica di costruzione permette di poter controllare la trasmissione del calore contando su un sistema di pressione superiore in modo da poter gestire il corretto trasferimento di calore indispensabile per poter ottenere una ottima qualità di cartone a qualsiasi velocità e composizione.
I piani caldi EXPRESS si compongono di una sezione iniziale calda che a sua volta è suddivisa in 3 sezioni ed una sezione di traino finale fredda, da cui deriva il termine 3+1. All'inizio della sezione calda è posizionato un preriscaldatore di 500 mm. di diametro ed un braccio avvolgitore per poter regolare la fasciatura della carta in ingresso, in maniera tale che questa possa riscaldarsi in accordo con le diverse velocità e grammature. La sezione calda è formata da piastre in ghisa sferoidale la cui fusione unica garantisce stabilità, scorrevolezza e ciò che più importa un uniforme trasferimento di calore su tutta la superficie di contatto per garantire un incollaggio uniforme ed adeguato al tipo di amido usato.
La piastra ha un peso di 1.200 kg ed una dimensione di 750 x 2600 mm. ed una altezza di 190 mm. La piastra, all'interno, reca una serpentina di cunicoli appositamente studiati per consentire una continua ed ottima fluidità del vapore eliminando la possibilità di condensa interna, riuscendo così ad ottenere una superficie esterna riscaldata omogeneamente indispensabile alla buona formazione del cartone.
La placca semirigida è supportata da un telaio che ha la particolarità di poter sostenere la placca alle estremità in maniera da evitare lo schiacciamento del bordo di cartone. Le scarpette sono supportate da un telaio suddiviso in tre sezioni ciascuna delle quali preme con pressione differente in accordo con il tipo di cartone lavorato e la velocità di lavoro ed il tipo di amido usato.
Il traino della striscia di cartone è formato da un sandwich a cinghie di elevato potere aggrappante, entro le quali è ben tenuto uniformemente la striscia di cartone. Il piano inferiore è costituito da piastre e da un sistema di pressione superiore costituito da uno scatolato la cui forma è stata progettata per non schiacciare il cartone e nel contempo fornire la pressione sufficiente a garantire il traino a qualsiasi velocità e grammatura del cartone.
Il feltro superiore ed inferiore sono trainati da due grossi tamburi motorizzati da due differenti motori in corrente continua di diversa potenza. I motori sono direttamente calettati sulla fiancata, e tramite ingranaggi trasmettono il moto ai tamburi di traino. Un sistema elettronico compara la velocità reale di entrambi, in maniera tale da avere una identica velocità di lavoro.
TAGLIERINA AUSILIARIA - ROTARY SHEAR CS
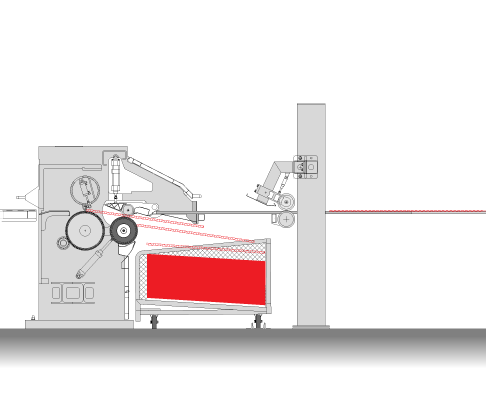
- Intro
- Gallery
Il cambio ordine CONSTANT SYSTEM (brevettato da Fosber) permette un reale cambio ordine senza interruzione della striscia di cartone, lavorando in abbinamento su due livelli di taglierina. I problemi dei cambi ordini convenzionali sono eliminati in quanto non si ha più la necessità di creare un GAP. Questa sequenza unica di cambio ordine è possibile solo utilizzando la Taglierina Ausiliaria CONSTANT SYSTEM ed il taglia-cordona TWIN della Fosber. La taglierina ausiliaria CONSTANT SYSTEM lavora come una comune taglierina ausiliaria lama /poliuretano, la sua costruzione è identica a quella di una rotary shear standard ad eccezione del coltello superiore segmentato in 26 lame retrattili le quali possono essere attivati individualmente secondo un pre-determinato schema di taglio eseguendo un taglio parziale sulla larghezza del cartone. L'asse inferiore è ricoperto da anelli aperti in poliuretano la cui chiusura è assicurata da incastri a "coda di rondine" per una facile sostituzione. La sezione di espulsione dello scarto è identica a quella della rotary shear standard, comprende un diverter, azionato pneumaticamente, un piano a cinghie motorizzato ed un rullo gommato di espulsione, oltre ad un rullo di pressione, rivestito da ruote no crush, avente lo scopo di guidare il cartone all'interno del diverter.
La taglierina ausiliaria CONSTANT SYSTEM può lavorare come una taglierina convenzionale, può scartare ed eseguire tagli completi per un cambio ordine convenzionale con GAP, oppure eseguire tagli parziali iniziando la sequenza di un cambio ordine CONSTANT SYSTEM. In un cambio ordine GAPless la taglierina ausiliaria CONSTANT SYSTEM rende attive solo le lame necessarie a produrre un taglio parziale centrale rispetto alla striscia di cartone, il quale è lungo quanto la distanza tra i tagli di divisione dell'abbinamento (twin) dell'ordine precedente e successivo, vengono inoltre attivate anche le lame laterali di divisione e raccordo del rifilo.
Quando il taglio parziale raggiunge il TWIN, la lama di divisione dell'abbinamento del nuovo ordine si abbassa in anticipo rispetto agli altri utensili, mentre quella del vecchio ordine si solleva in ritardo sempre rispetto agli altri utensili. Le lame di divisione dei due abbinamenti si sovrappongono intersecando il taglio parziale prodotto dalla taglierina ausiliaria CONSTANT SYSTEM. In questa maniera, il cambio ordine CONSTANT SYSTEM Fosber, mantiene unito il vecchio ed il nuovo ordine senza generare frammenti, assicurando continuità di flusso e senza nessuna variazione di velocità. L'ondulatore è finalmente una macchina continua. Questo elimina problemi associati ai cambi ordine tradizionali con GAP quali: riduzione di velocità per cambio ordine, accelerazione elevata del vecchio ordine, jam-up dovuti allo sbandamento del cartone, gobbe, errori di taglio dovuti alle brusche accelerazioni, nessun cambio di rilevazione di misura. Il rischio dei jam-up è eliminato.
TAGLIA CORDONA - TWIN
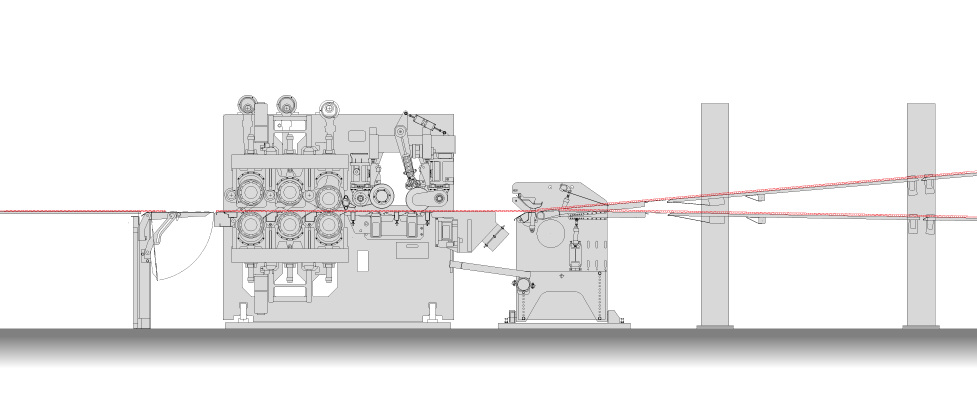
- Intro
- Gallery
Il nuovo taglia cordona Fosber TWIN è una macchina molto compatta, a bassa manutenzione, costituita da 2 coppie indipendenti di taglio e cordonatura che permettono di poter effettuare cambi ordine, sia GAP che NO-GAP senza limiti di velocità. L'accurato e veloce posizionamento degli utensili è affidato a 3 Robot indipendenti che si muovono su una cremagliera il cui impiego garantiscono prestazioni, precisione ed affidabilità.
La macchina, a seconda delle esigenze del Cliente, può essere configurata con il sistema di taglio a rasoio sia dal basso che dall'alto. Grazie all'impiego di coltelli in carburo di tungsteno, che garantiscono una qualità di taglio superiore senza bisogno di essere lubrificati, la macchina riesce ad avere un perfetto profilo di taglio con qualsiasi tipo di carta e composizione. Il sistema di affilatura automatica è unico per entrambi gli assi ed è composto da una coppia di mole folli montate a bordo del Robot coltelli.
I bassi costi di manutenzione sono stati raggiunti grazie all'introduzione dell'innovativo sistema di taglio che prevede l'impiego, come contrasto alla lama, di una serie di barre in Teflon che vengono periodicamente spostate dal sistema automatico di gestione.
I due assi di cordonatura (gemelli) possono essere equipaggiati con diversi profili di cordonatura per aumentare la versatilità di produzione e poter lavorare contemporaneamente, senza l'ausilio di alcun asse di cordonatura ausiliario, 2 profili differenti di cordoni ricorrendo al posizionamento TANDEM dei cordoni.
La macchina può essere equipaggiata con un numero di coltelli per poter lavorare fino a 8 scatole per asse. Per un numero di tagli superiore la macchina ricorre automaticamente al posizionamento TANDEM dei coltelli, utilizzando gli utensili dell'altro asse di taglio. Questo è possibile anche grazie al comando individuale di ciascuna delle lame; prerogativa che permette sia di ottimizzare la durata che di poter escludere un coltello in caso di necessità senza dover fermare la macchina.
I robot di posizionamento sono controllati con motori Brushless direttamente calettati su riduttori epicicloidali che, in abbinamento alla cremagliera, permettono di poter raggiungere elevate velocità di traslazione con un'alta precisione di posizionamento. Per aumentare l'affidabilità della macchina., alla fine di ogni posizionamento, il robot coltelli effettua una veloce scansione della posizione degli utensili.
TAGLIERINA TRASVERSALE - MASTER
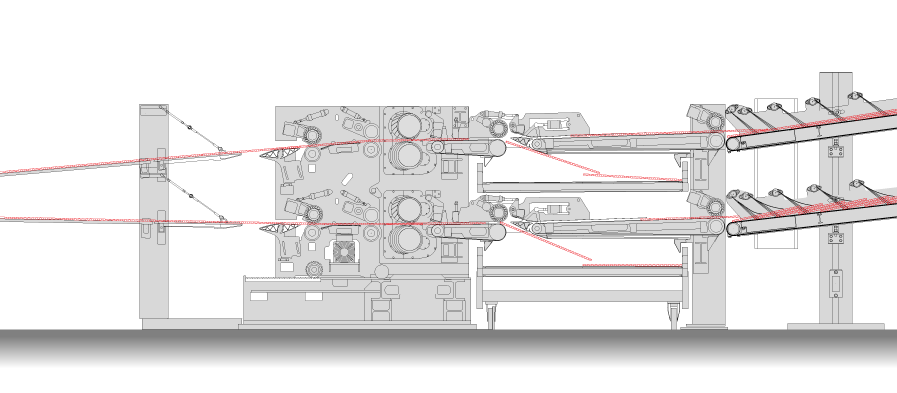
- Intro
- Gallery
La taglierina trasversale MASTER consta di tre sezioni principali - la sezione d'ingresso, la sezione di taglio e la sezione d'uscita. La sezione di ingresso consiste in un piano oscillante di supporto al cartone ed una coppia di rulli di traino motorizzati. La sezione d'ingresso può traslare per permettere un facile accesso al corpo macchina facilitando le operazioni di manutenzione in piena sicurezza.
La sezione di taglio consiste in una coppia di rulli a bassa inerzia con tecnologia a cuscinetto idrostatico, su cui sono montate le lame che non necessitano lubrificazione (OIL-FREE). Il profilo elicoidale delle lame genera un taglio dolce e progressivo riducendo gli sforzi e consentono l'utilizzo di cilindri sottili a bassa inerzia e tali da permettere prestazioni elevate oltre a rapide ed istantanee variazioni di taglio. La rotazione delle camicie è garantita da ingranaggi in presa diretta tra loro calettati in testa a ciascun rullo. Grazie ai nuovi cuscinetti idrostatici, a un nuovo telaio e al nuovo design delle fondamenta della macchina, le vibrazioni sono enormemente ridotte.
La sezione di uscita può essere dotata di un sistema di scarto per ciascun livello per espellere automaticamente gli scarti generati dal cambio ordine e tutte le giunte, mantenendo costante la velocità. Il sistema espelle anche i fogli di preprint fuori registro e qualsiasi imperfezione rilevata dal Pro/Quality, garantendo il 100% di prodotto vendibile di qualità. Gli scarti vengono deviati su un convogliatore che scarica lateralmente (lato operatore o lato motori o entrambi). Ciò significa che i controlli dei fogli possono essere eseguiti in modo semplice e sicuro in qualsiasi momento, riducendo significativamente il bisogno di manodopera e il carico di lavoro sullo stacker e sulle passerelle. Il sistema di deviazione rifiuti ha un design a cassetta che consente di estrarlo completamente dalla macchina per una manutenzione molto più facile.
La Master può anche essere dotata di un sistema di "digital ready" auto-posizionante per la gestione di carte prestampate. Il sistema si allinea automaticamente sul segno di taglio e può essere configurato per la lettura sia superiore che inferiore. Gli ordini preprint possono essere eseguiti in modo completamente automatico, con diversi ordini di prestampato eseguiti simultaneamente su ciascun livello, con scarti praticamente nulli e senza la necessità di intervento da parte dell'operatore. Per soddisfare differenti necessità di produzione, la taglierina trasversale MASTER è disponibile in diversi modelli che differiscono per prestazioni e numero di motori installati. Tutti i motori di azionamento sono motori brushless AC e la precisione di taglio è garantita attraverso un Vector Drive Control.
Tutte le versioni sono dotate di un sistema di recupero di energia, che riduce fortemente i consumi. La taglierina trasversale MASTER è gestita attraverso un sistema di controllo ad alte prestazioni, attraverso il quale è possibile visualizzare i dati di ordine, lo stato della macchina, i dati di produzione. Il sistema di gestione permette inoltre alla MASTER di comunicare con le altre macchine del dry-end e di comunicare in rete con altri sistemi di programmazione, come ad esempio l'accesso remoto via modem o di rete di connessione per il servizio di supporto e di diagnostica Fosber. La sicurezza dell'operatore sulla taglierina trasversale MASTER è garantita con l'adozione di dispositivi di protezione e di interblocco tali da soddisfare la totalità degli standard governativi mondiali e delle Società più rigide.
IMPILATORE - TERMINAL
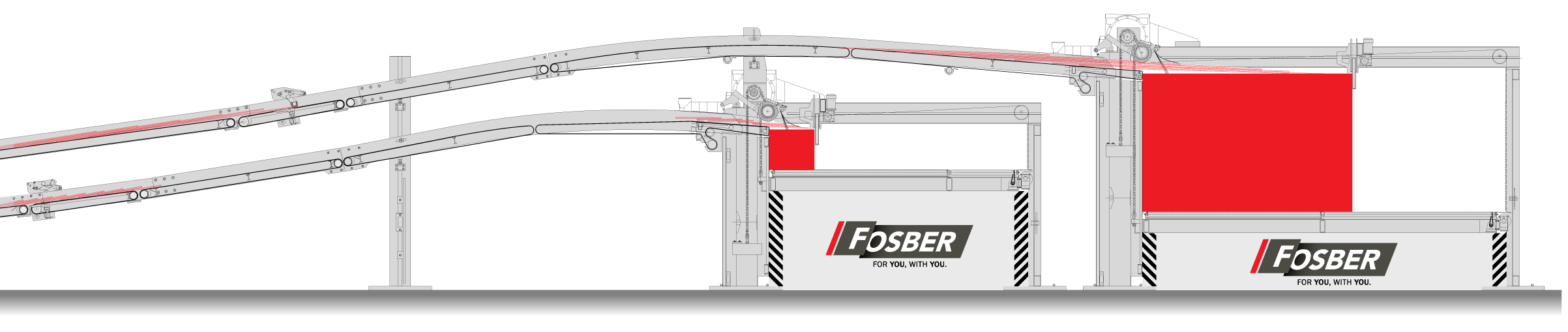
- Intro
- Gallery
Il nuovo raccoglitore Fosber TERMINAL è composto dalle sezioni di trasporto, una di frenatura e separazione, ed una piattaforma di scarico di tipo Down-Stacker.
La sezione di raccolta dei fogli provenienti dalla taglierina prevede un tappeto con guide ed un'aspirazione nella prima sezione che, abbinato alla gestione delle spazzole di frenatura, garantisce un'ottima qualità di impilamento fin dall'ingresso in macchina del cartone. Le spazzole di frenatura sono controllate dinamicamente in base al formato (lunghezza e larghezza), alla resa, al tipo d'onda ed alla velocità seguendo una curva di pressione personalizzata.
La separazione delle pile e degli ordini è affidata ad una pinza mobile che permette di effettuare cicli d'espulsione ad altissime velocità alla massima qualità disponibile sul mercato.
L'accurato controllo della piattaforma permette di ottenere un'ottima qualità di formazione della pila alle massime prestazioni con qualsiasi tipo di prodotto e formato. Quest'ultimo risultato è stato raggiunto grazie all'introduzione di un sistema innovativo nel suo genere che permette di poter modulare l'inclinazione dell'ultima sezione di trasporto in relazione alle dimensioni del formato ed il tipo d'onda. Il nastro con cui è equipaggiata la piattaforma, permette di scaricare anche i formati di cartone più difficili senza dover rinunciare né alle prestazioni né alla sicurezza degli operatori. L'aspetto sicurezza è stato particolarmente curato in quanto la macchina è stata progettata con riferimento alla norma di settore EN 1010-5:2005 che prevede l'impiego, tra gli altri elementi, di una doppia catena di sicurezza e di uno scanner anti-intrusione.
Il raccoglitore Fosber TERMINAL, grazie al suo programma dinamico che riesce ad adeguarsi ad ogni condizione di lavoro, assicura un'eccellente qualità con tutti i tipi di cartone e formato.
SUPERVISOR - Pro/Syncro

- Intro
- Gallery
Pro/Syncro è il supervisore di linea che Fosber ha progettato per controllare ogni tipo di ondulatore.
Può essere fornito sia come controller della parte umida (wet-end), della parte secca (dry-end) o di entrambe.
Le features di Pro/Syncro per la parte wet-end includono la gestione e la calibrazione della scorta ponte, la sincronizzazione delle giunte, la stampa delle etichette bobine parzialmente utilizzate, l'interfaccia per la gestione dello stock di bobine, la gestione dei portabobine, i controlli rottura carta, i cambi ordine e tutta la diagnostica macchina per macchina.
Per la parte dry-end invece Pro/Syncro offre dettagliati report di produzione, diagnostica intelligente, stampa cartellini bancale, interfacce al wet-end, alla rete uffici, al plant management system ed alla movimentazione.
Pro/Syncro può essere inoltre ulteriormente implementato per gestire il process control.
Concretamente Pro/Syncro è composto da una consolle di comando, solitamente posizionata in control room, e da una serie di rilevatori posizionati sulle macchine.
In opzione è possibile aggiungere una serie di stazioni di comando aggiuntive, posizionabili lungo la linea, per potere controllare Pro/Syncro anche al di fuori della control room.
L'architettura di Pro/Syncro è basata su due diversi network, a cui sono connessi tutti gli apparati hardware distribuiti sulle macchine. Un network è dedicato a tutti i sistemi che consentono a Pro/Syncro di sincronizzare le macchine tra di loro e controllare l'avanzamento della produzione in tempo reale.
L'altro network consente a Pro/Syncro di dialogare con le altre reti presenti in fabbrica.
Le funzioni di Pro/Syncro possono essere personalizzate per rispondere alle esigenze specifiche di ogni impianto.
Pro/Active
Il controllo di processo Pro/Syncro è un sistema a ciclo chiuso che monitora e controlla automaticamente tutti i differenti setting e variabili del processo di produzione del cartone ondulato riducendo gli scarti, assicurando che sia realizzato un perfetto incollaggio e prodotto un cartone perfettamente piatto di elevata qualità. Il sistema misura e monitora le temperature ed i livelli di umidità in posizioni strategiche lungo la linea ondulatrice e adatta automaticamente le varie macchine e i parametri inseriti a sistema per assicurare che siano raggiunti i setting ideali programmati ed individuati per le tipologie di cartone che lo stabilimento produce.
Il controllo di processo esegue automaticamente un adattamento continuo di tali variabili come il setting del posizionamento dell’angolo di avvolgimento della carta, della pressione del vapore lungo l’ondulatore, delle docce di vapore, di tutti gli spessori della colla, i setting della pressione del vapore nelle scarpette dei piani caldi così come la tensione della carta nel freno ponte della giuntatrice. Il sistema di controllo a ciclo chiuso consente, inoltre, di correggere istantaneamente in automatico eventuali distorsioni del cartone, imbarcamenti, (rilevati da un operatore o da una barra laser) sia longitudinali e trasversali.
La pagina principale di interfaccia operatore è semplice e intuitiva e riporta non soltanto tutti i parametri correnti ma consente anche all’operatore di regolare ed adeguare velocemente i setting per ciascuna delle differenti qualità di carte impiegate. Se si desidera, tali regolazioni e setting, possono facilmente essere salvate all’interno di un database.
Il record è una funzione avanzata del controllo di processo, è uno strumento molto utile per raccogliere e conservare (fino a 12 mesi) lo storico di tutte le produzioni e i dati di processo per ogni ordine dry-end realizzato dall’ondulatore. Tale funzione, registra e genera dei grafici per l’analisi dei dati rilevanti come velocità di produzione, angolo id avvolgimento carta, temperature e umidità rilevate, livelli di amido, impostazione delle scarpette, ecc…, in modo che i setting obiettivo possano essere continuamente monitorati, verificati e ottimizzati. Inoltre, il record offre ai nostri clienti, così come ai loro rispettivi clienti, una tracciabilità completa di ogni singolo ordine prodotto dal dry-end negli ultimi 12 mesi.
La flessibilità e la varietà di funzioni contenute all’interno di Pro/Syncro costituiscono un potente strumento che aumenta significativamente la produttività e la qualità del prodotto finito dell’ondulatore e offre la possibilità di individuare degli standard di produzione per differenti stabilimenti appartenenti allo stesso gruppo. Il miglioramento delle performance ottenuto tramite Pro/Syncro, consente, inoltre, di diminuire i costi grazie alla riduzione degli scarti, del consumo di amido e vapore e delle contestazioni da parte dei clienti.
CONTROLLI AVANZATI

- Intro
- Gallery
Introducendo il suo ultimo sistema software per migliorare le prestazioni, Fosber lancia Pro/Care e Pro/Quality per l’ultima generazione dei propri ondulatori.
Mentre l’industria del cartone ondulato inizia il suo viaggio verso “l’Industria 4.0”, Fosber sta cercando modi per progettare macchine a prova di futuro.
Con attenzione alla progettazione di macchinari intelligenti, Fosber si concentra sui sistemi software che aiuteranno ad assicurare il massimo tempo di produzione ed il minimo tempo di inattività nella routine giornaliera ed una migliore qualità del cartone, con la sua ultima generazione di linee, Fosber ha presentato Pro/Care e Pro/Quality.
Pro/Care
Il concetto alla base del Pro/Care è di rimuovere la totale dipendenza dalle persone di questo aspetto vitale per la manutenzione dell’ondulatore, essendo la macchina stessa a segnalare esattamente quali interventi debbano essere eseguiti.
Monitorando continuamente produzione, processi e dati in tempo reale, Pro/Care è in grado di organizzare intelligentemente e scientificamente la manutenzione e suggerire il supporto tecnico necessario, ma è anche in grado di fornire diagnostiche preventive ed una analisi dei dati senza precedenti.
Basandosi sui dati di produzione acquisiti e all'utilizzo della linea, Pro/Care identifica, pianifica e suggerisce le attività di manutenzione in sospeso che devono essere eseguite e quando.
Pro/Care identifica esattamente quali risorse, ore-uomo, equipaggiamento e pezzi di ricambio sono richiesti per procedere con la manutenzione programmata.
Le funzioni di ricerca interattiva consentono agli utenti di individuare e consultare immediatamente le procedure di manutenzione anche quando lavorano fisicamente all'interno della macchina grazie alla comoda accessibilità tramite tablet o smartphone sulla rete WiFi dedicata.
Questa funzione del Pro/Care è stata sviluppata non solo come prezioso sistema di manutenzione intelligente on-line, ma anche come strumento di training, per permettere agli operatori di migliorare costantemente la loro conoscenza della linea, grazie alle sue funzioni interattive.
La suite di software analitico avanzata offre registrazioni e report dei processi di produzione grazie alla sua interfaccia completa e all'integrazione con il sistema di controllo Pro/Syncro.
Filtri flessibili e funzioni di report forniscono analisi dettagliate su qualsiasi periodo desiderato negli ultimi 12 mesi: tipi di onda, qualità del cartone, macchine, parametri, tempi di inattività, cambi, ordini, formati, peso delle carte, velocità etc.
Due moduli aggiuntivi di Pro/Care monitorano e registrano continuamente importanti dati di consumo sia a scopo diagnostico che analitico. Il modulo CMD (Corrugator Machine Diagnostics) controlla costantemente tutti i motori principali e le loro catene cinematiche associate, incrociando simultaneamente questi dati con le condizioni di marcia effettive e il tipo di produzione in corso. Il sistema stabilisce una matrice di correlazione di auto-apprendimento tra il consumo corrente misurato di tutte le catene cinematiche rispetto ai parametri effettivi dell’ondulatore.
In questo modo, fornisce analisi diagnostiche in tempo reale poiché è in grado di identificare immediatamente eventuali anomalie che si verificano al di fuori delle prestabilite bande di tolleranza. Tutto ciò fa sì che il Pro/Care notifichi e attivi automaticamente il servizio clienti di Fosber, consentendo di identificare e affrontare potenziali problemi attraverso misure preventive prima che diventino problemi reali.
Allo stesso modo, il modulo CCM (Corrugator Consumption Monitoring) misura i consumi effettivi di vapore, energia elettrica, aria compressa e il consumo di amido durante il funzionamento dell’ondulatore, che vengono incrociati in tempo reale con il tipo di cartone in produzione. Questi valori sono registrati e memorizzati in Pro/Care e sono utili, non solo per ulteriori diagnosi della macchina, ma per una post-valutazione per un'analisi completa dell'ottimizzazione dei costi, dell'uso di energia e della sostenibilità generale. Grazie alla programmazione della manutenzione on-line scientifica ed intelligente, al monitoraggio ed alla registrazione in tempo reale, all'aumento dell'analisi dei dati e alla diagnostica preventiva, Pro/Care può aiutare a massimizzare il tempo di attività e l'efficienza complessiva dell’ondulatore.
Pro/Quality
Pro/Quality è un sistema di rilevamento e monitoraggio dei difetti installato su ogni single facer per verificare immediatamente il cartone, all’origine, appena esce dalla macchina prima della scorta ponte.
Utilizzando tecniche e tecnologie di visione, Pro/Quality monitora, rileva e registra in tempo reale eventuali difetti su tutta la larghezza del cartone con una copertura del 100 percento. Rileva tutte le imperfezioni della superficie, come difetti della carta, e tutti i difetti 3D come delaminazione, bolle, pieghe, grinze, strappi, giunte, schiacciamento dell’onda o difetti del bordo. Grazie alla sua integrazione con Pro/Syncro, Pro/Quality traccia e scarta automaticamente ogni foglio difettato immediatamente dopo la taglierina ausiliaria o trasversale. In questo modo, solo il cartone vendibile passa all’impilatore. Pro/Quality prevede anche un’alert e regola istantaneamente i parametri rilevanti delle macchine e le impostazioni del processo per correggere il difetto rilevato.
Pro/Quality non solo ottimizza la qualità del cartone e riduce gli sprechi, ma garantisce anche che nessun foglio difettato venga spedito al proprio cliente.
SOUND BOOTH

- Intro
- Gallery
Fosber ha sviluppato una cabina insonorizzata su misura per l’ondulatore completo con un design nuovo dalle linee moderne e razionali. Un design senza precedenti nel settore del packaging che conferisce all’ondulatore un aspetto unico e contemporaneo. La nuova insonorizzazione sarà sinonimo di tecnologia, innovazione, professionalità e attenzione al dettaglio per chiunque visiterà la vostra area produttiva.
La nuova cabina insonorizzante riduce le emissioni di rumore al di sotto di 85 db e risponde alle più recenti normative Europee. Grazie a tale tecnologia, una linea ondulatrice potrebbe essere installata in prossimità di zone residenziali senza limitazioni di orario per la produzione.
La cabina insonorizzata è stata ingegnerizzata utilizzando una combinazione di ampie aree di vetro temperato e panelli insonorizzanti che consentono di ridurre i livelli di rumore mantenendo un’ottima visibilità sulle macchine in funzione (un aspetto che non è tenuto in considerazione dalle normali cabine insonorizzanti).
Dotata di illuminazione interna e sistemi di estrazione, la cabina insonorizzata è il risultato di una progettazione ed ingegnerizzazione “su misura” sull’ondulatore Fosber, e per questo, totalmente integrata nei comandi, l’operatore può gestire il processo di produzione direttamente su pannelli di comando riportati esternamente sulla cabina, senza necessità di accedere all’interno. Consente, inoltre, un accesso facile e senza limiti dell’operatore per la manutenzione quando si renda necessario.