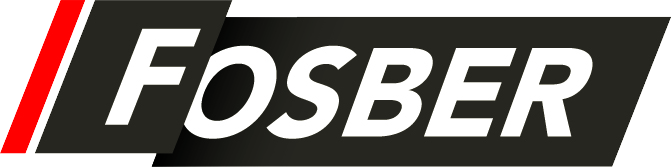

Fosber's Supervisor systems: more precision, more control
Fosber's Supervisors
Fosber presents its latest performance enhancing software systems: Syncro, Process Control Supervisor, Pro/Care and Pro/Quality.
As the corrugated industry begins its journey into ‘Industry 4.0’, equipment manufacturers are looking at ways to future proof machinery designs.
With the emphasis on designing intelligent machinery, Fosber is now focussing its attention on software systems that will help ensure maximum uptime and minimum disruption to daily routines and enhanced quality of corrugated board.
Syncro
Fosber's corrugator is controlled by the Syncro supervisor system. Syncro can be supplied either as a pure wet-end control system, a pure dry-end control system or a total corrugator control system.
Automatic wet-end features of Syncro include bridge management and calibration, synchronisation of speed and splices, partial reel label printing, roll stock management interface, roll stand monitoring, paper break detection, wet end order change as well as full displays for machine status, alarms and diagnostics.
Fosber's Syncro dry-end control supervisor provides detailed production reporting, intelligent diagnostics, pallet label print-outs, and data links to the wet-end, office and scheduling networks, and materials handling control systems.
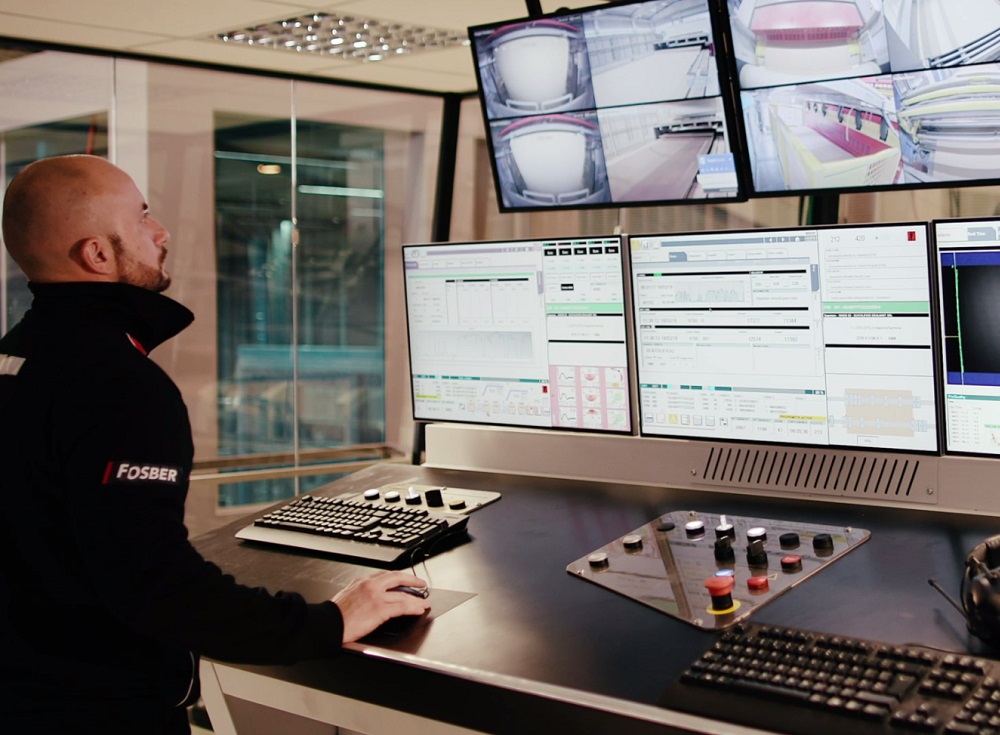
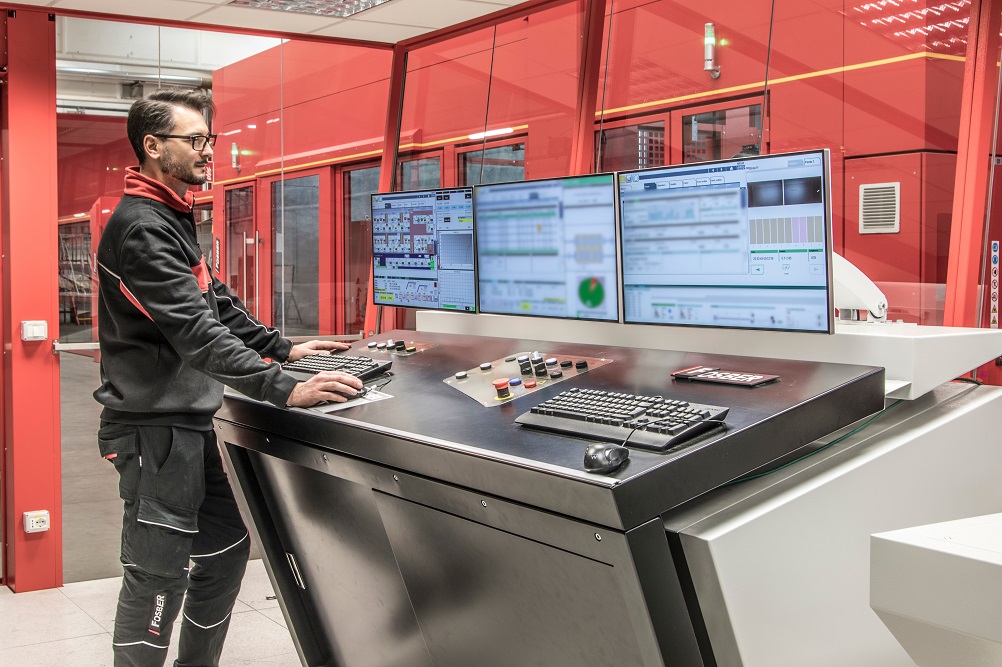
Process Control Supervisor
Process Control Supervisor (PCS) is a closed-loop control system that automatically monitors and controls all the various settings and variables of the corrugating process, reducing waste by ensuring a proper bond and optimum quality flat board is produced.
This is achieved by measuring and monitoring temperatures and moisture levels at strategic positions long the corrugator line, and then automatically adapting the various machine and system parameters to ensure that the ideal target process settings that have been set and personalised for each individual board type quality the plant produces are met.
The PCS will therefore continuously automatically set and adjust all such settings such as the variable wrap arm positions, steam pressures along the corrugator, steam showers, all glue gaps, double backer steam shoe pressure settings as well as the paper tensions in the splicers and at the bridge brake. The closed-loop control system also allows instant automatic correction of any warp detected (either by the operator or by automatically by a laser bank) in either machine or cross-machine direction system.
The Data Traceability Supervisor (DTS) feature is a further enhancement to the PCS and an extremely useful tool that collects & stores (for up to 12 months) all the historical production & process data for every single dry-end order run off the corrugator. This feature records, stores & generates graphs of all relevant data so target settings can continuously be monitored, checked and optimised. Furthermore DTS provides our customers, as well as their own subsequent customers, with a complete “provenance” of every individual packaging order produced on the dry-end over the last 12 months.
Pro/Care
The core concept of Pro/Care is to remove the total reliance of this vital aspect of maintenance of the corrugator on people, by having the machine itself dictate exactly which services are needed to be carried out.
By continuously capturing actual production, process and machinery data in real time, Pro/Care is able to intelligently and scientifically manage the maintenance and technical support, as well as providing pre-emptive diagnostics and unprecedented data analysis. Based on the actual captured production data and usage of the corrugator, Pro/Care identifies, plans and instructs which pending maintenance tasks need to be carried out and when.
Pro/Care details exactly which resources, man hours, equipment and parts are required to carry out the scheduled maintenance. It illustrates the relevant step-by-step procedures through easy-to-follow video and photographic instructions and generates both maintenance reports and proposals for new and future activities.
Additional modules:
- The CMD (Corrugator Machine Diagnostics) module constantly monitors all the main motors and their associated kinematic chains, simultaneously cross referencing this data with the actual running conditions and type of production on the corrugator. The system establishes a self-learning correlation matrix between the measured current consumption of all the kinematic chains against the actual parameters of the running corrugator. In this way, it provides real time diagnostic analysis as it is able to instantly identify any anomalies. This results in Pro/Care automatically notifying and activating the Fosber customer care dept. allowing potential issues to be indentified and addressed though pre-emptive measures before they become actual problems.
- The CCM (Corrugator Consumption Monitoring) module measures actual steam, electrical power, compressed air and starch consumption during operation of the corrugator, which is cross referenced in real time with the type of board production currently running. These values are recorded and stored and are useful, not only for further machine diagnostics but allowing post-evaluation for a complete analysis of cost optimisation, energy usage and overall sustainability. Thanks to scientific and intelligent on-line maintenance programming, real time monitoring and recording, enhanced data analysis and pre-emptive diagnostics, Pro/Care assists in maximising the uptime and overall corrugator efficiency.
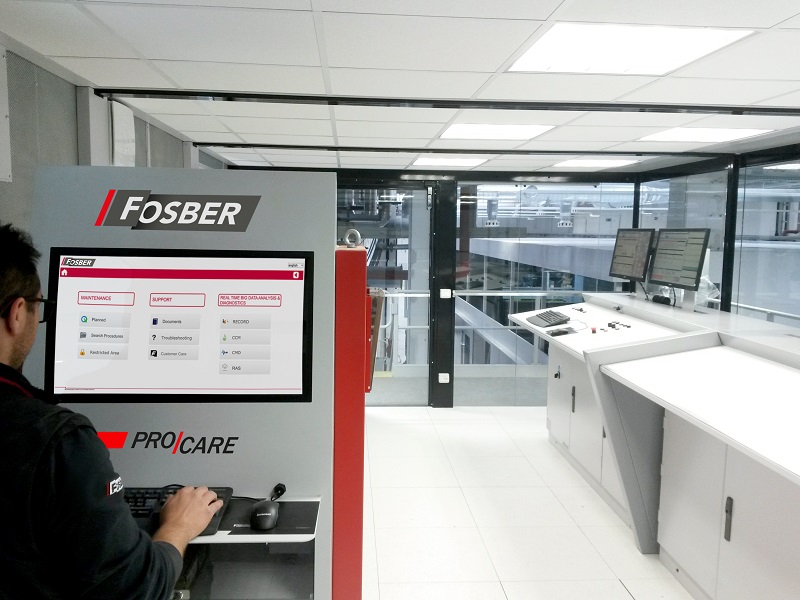
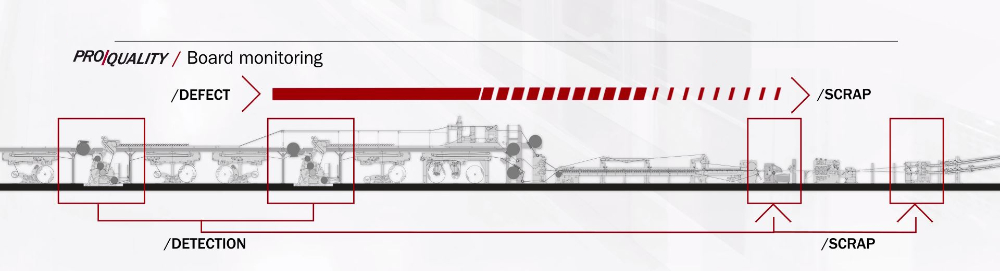
Pro/Quality
Pro/Quality is a defect detection and monitoring system that is installed at each single facer to monitor the web immediately, at source, as it exits the machine just prior to the take-up conveyor. Utilising vision techniques and technologies, Pro/Quality monitors, detects and records in real-time any defects across the full web width with 100 per cent coverage.
It detects all web surface defects such as paper defects, as well as any 3D defects such as delamination, bubbles, blistering, folds, wrinkles, tears, splice joints, flute crush or edge defects. The system is intrinsically linked to Fosber’s Syncro corrugator control and wet-end process control system to exchange all relevant production and process information of the running order, thus providing a useful analytical database and record of all defects created, cross referenced against this data.
Thanks to its integration with Syncro, Pro/Quality automatically tracks and ejects any detected waste sheets from the corrugator at the waste diverter located immediately after the cut-off knife. In this way, only sellable boards are passed on to the stacker. Pro/Quality also provides instant operator diagnostics and immediately adjusts relevant machine parameters and process settings to correct the detected defect.
Pro/Quality not only optimises board quality and reduces waste but it also guarantees no defective board from the corrugator is delivered to the plant’s customer.